CivicCanuck
Well-Known Member
Added some pictures to my build thread, and figured I should make a DIY on how to make a good solder joint.
Tools of the trade: Solder, soldering iron, heat gun, heat shrink tubing in various sizes, electrical tape, wire cutters, wire strippers, olfa knife and 18 gauge primary wire.
Strip back about 3/4" of the insulation of the wires you are joining.
Install heat shrink tubing over the wire, and twist the bare ends tightly together.
This is what the wires should look like when twisted together tightly, with no loose strands, resulting in a connection that you can pull on slightly without the twist coming apart.
It is important to clean the tip thoroughly between solder joints, a damp sponge works well for this, I didn't have one but heating the tip up and applying new solder to it before making a joint cleans the tip as well.
Apply the clean, hot tip to the wire joint, and let the heat from the tip warm the joint, once the joint has reached the correct temperature, apply solder. In order to make a nice joint that isn't cold, the wire should melt the solder, not the tip.
After letting the completed joint cool ( should be nice and shiny, not dull which would indicate a slushy, cold solder joint ) slide the heat shrink tubing over the joint, making sure it's centered and apply heat from heat gun. The completed joint should look nice and smooth, and if you used the correct size heat shrink tubing there should be no gaps between the tubing and the wire jacket.
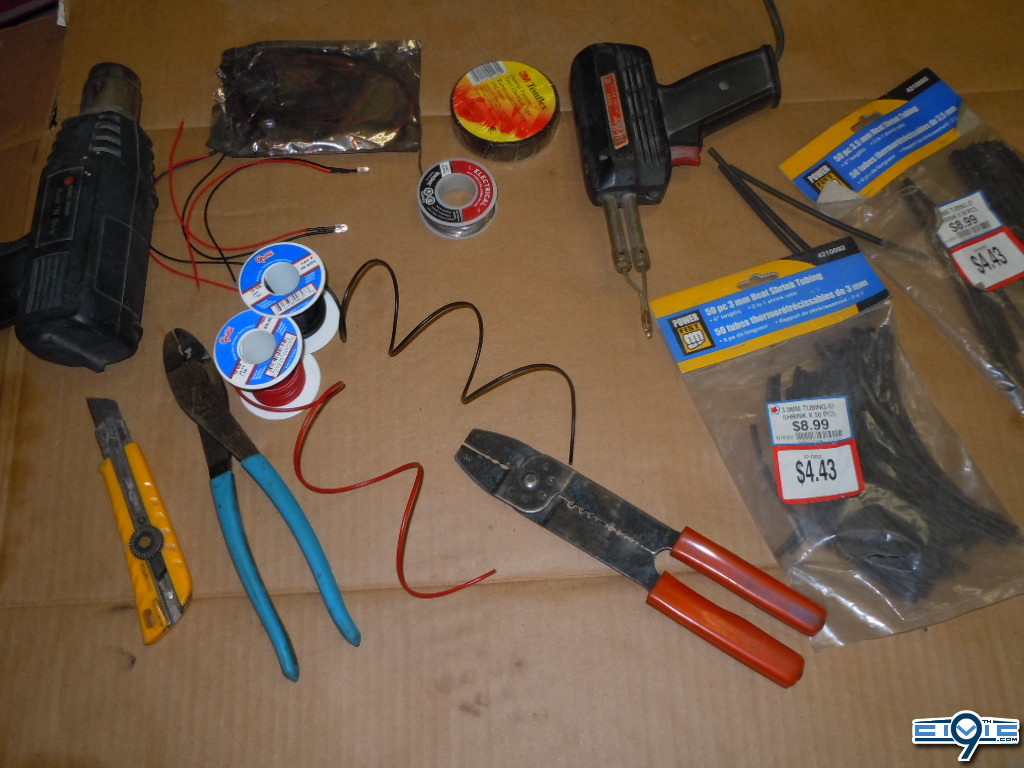
Tools of the trade: Solder, soldering iron, heat gun, heat shrink tubing in various sizes, electrical tape, wire cutters, wire strippers, olfa knife and 18 gauge primary wire.
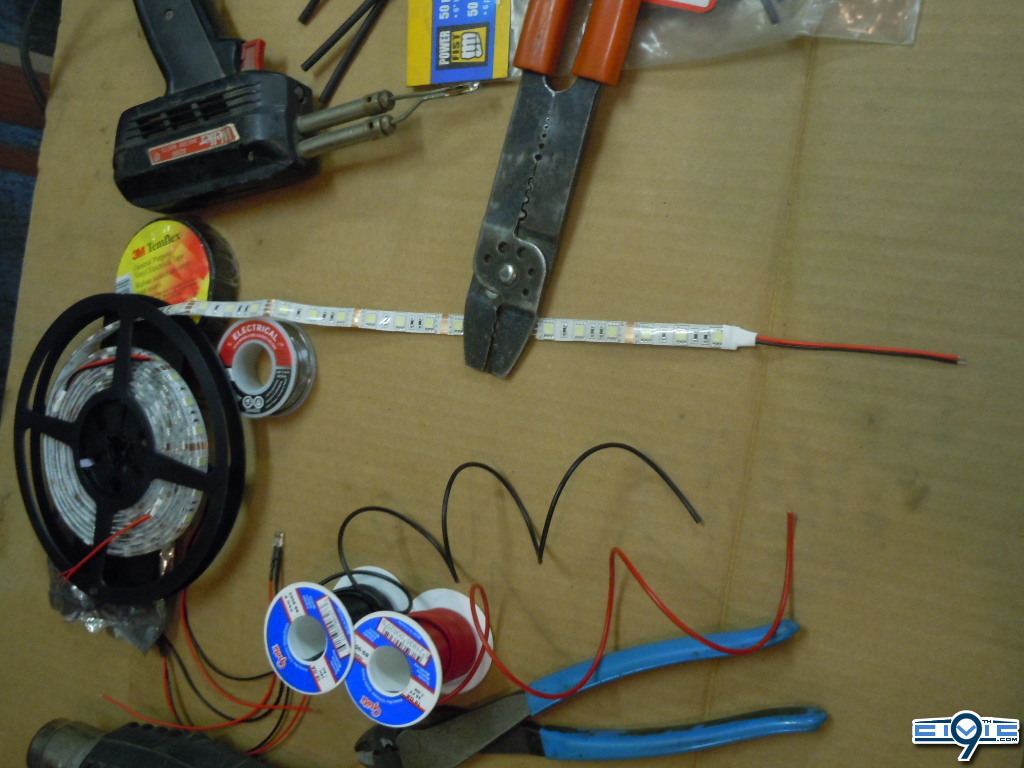
Strip back about 3/4" of the insulation of the wires you are joining.
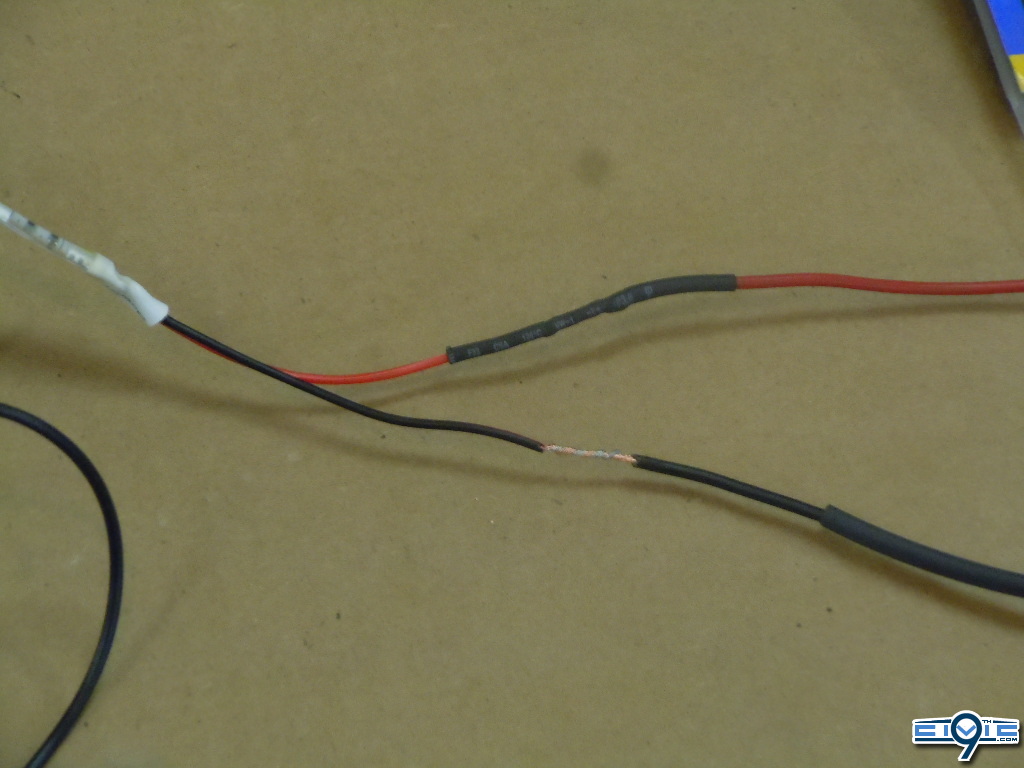
Install heat shrink tubing over the wire, and twist the bare ends tightly together.
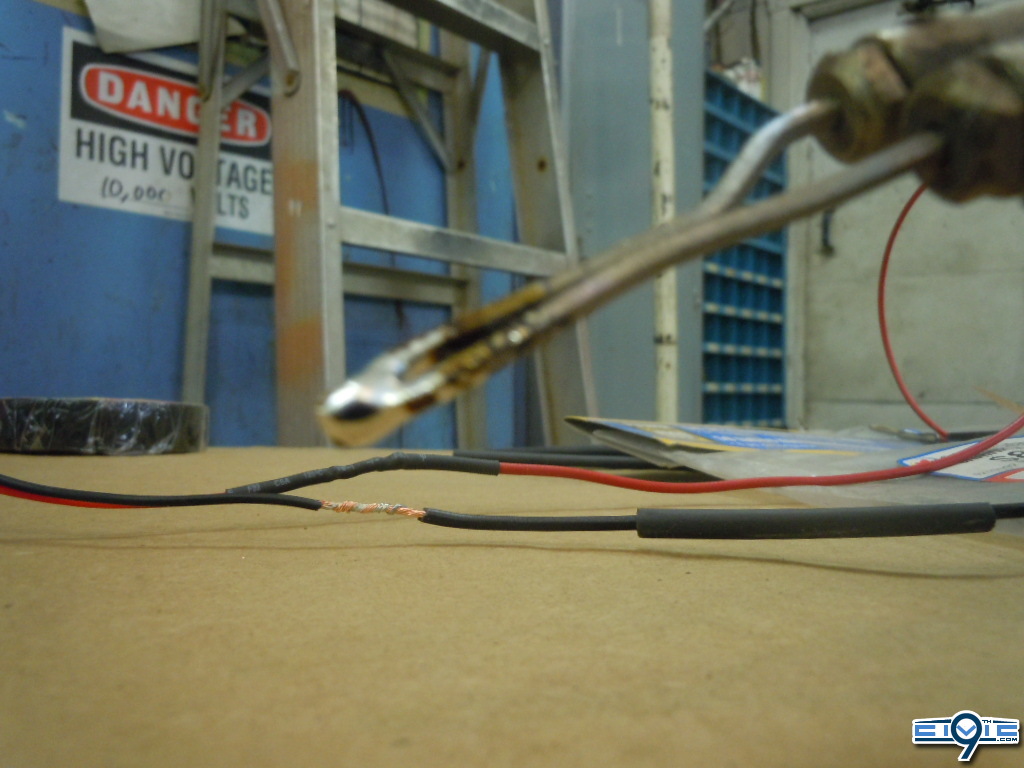
This is what the wires should look like when twisted together tightly, with no loose strands, resulting in a connection that you can pull on slightly without the twist coming apart.
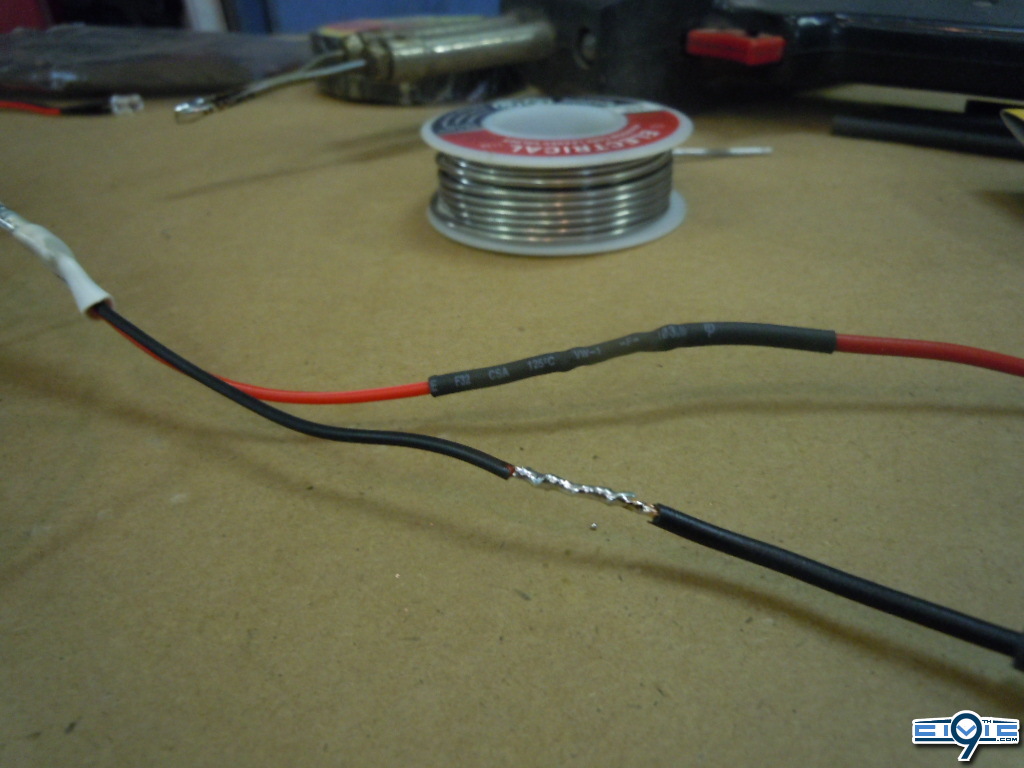
It is important to clean the tip thoroughly between solder joints, a damp sponge works well for this, I didn't have one but heating the tip up and applying new solder to it before making a joint cleans the tip as well.
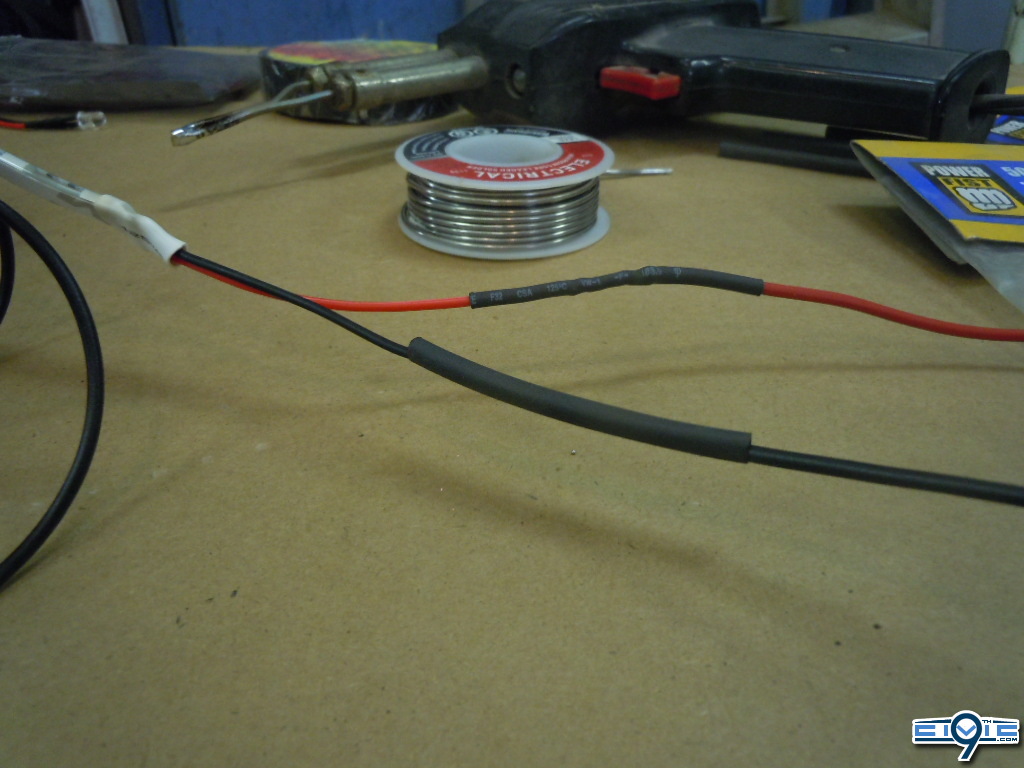
Apply the clean, hot tip to the wire joint, and let the heat from the tip warm the joint, once the joint has reached the correct temperature, apply solder. In order to make a nice joint that isn't cold, the wire should melt the solder, not the tip.
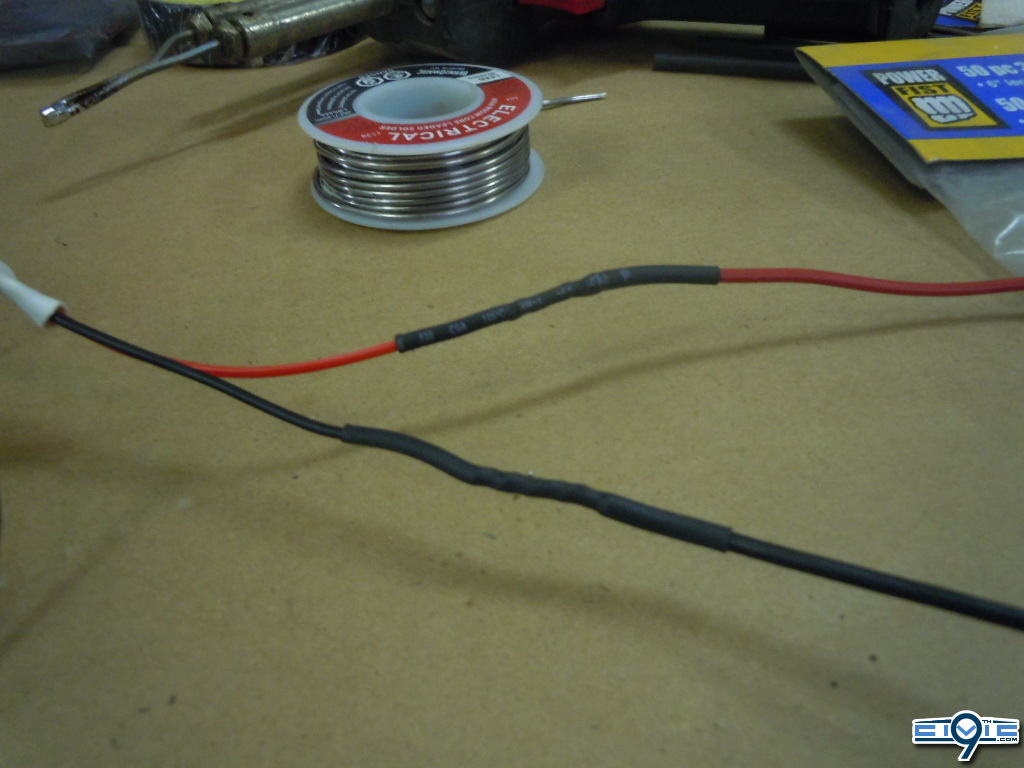
After letting the completed joint cool ( should be nice and shiny, not dull which would indicate a slushy, cold solder joint ) slide the heat shrink tubing over the joint, making sure it's centered and apply heat from heat gun. The completed joint should look nice and smooth, and if you used the correct size heat shrink tubing there should be no gaps between the tubing and the wire jacket.
Last edited by a moderator: